
From now on, the moves are only possible inside the printer cube defined in the printer settings. After that the color turns black, telling you the position is known. Press the home button to move the extruder to its defined position. Red means the host has no idea where the extruder really is. At the top you see the current extruder position. When you hover over the arrow, you will see a distance appear in mm, telling you how large the move will be. With the arrow keys you move the extruder in any direction. The next block controls the positioning of the extruder. If the “Easy Mode” is enabled, this field is not displayed. With the cursor up/down keys you can move through the history of manually send commands. Enter it and press return or hit the send button. The next row allows it to send any g-code command you like. At the top you see the most important printer status, so you always know what is happening. Max.When you turn your printer on, you will often come to this tab. The following table gives the various voltage specifications for the GPIO pins, it was extracted from the Compute Module datasheet here.Ī Hysteresis enabled b Default drive strength (8mA) c Maximum drive strength (16mA) wiringPi and GPIO connection overview Pad control, such as drive strength or Schmitt filtering, still applies when the pin is configured as an alternate function. Peripheral blocks internal to BCM2835 can be selected to appear on one or more of a set of GPIO pins, for example the I2C busses can be configured to at least 3 separate locations. Alternative functionsĪlmost all of the GPIO pins have alternative functions.

Asynchronous detection bypasses this synchronisation to enable the detection of very narrow events. At the system clock frequency, the pin is sampled with the criteria for generation of an interrupt being a stable transition within a three-cycle window, i.e.
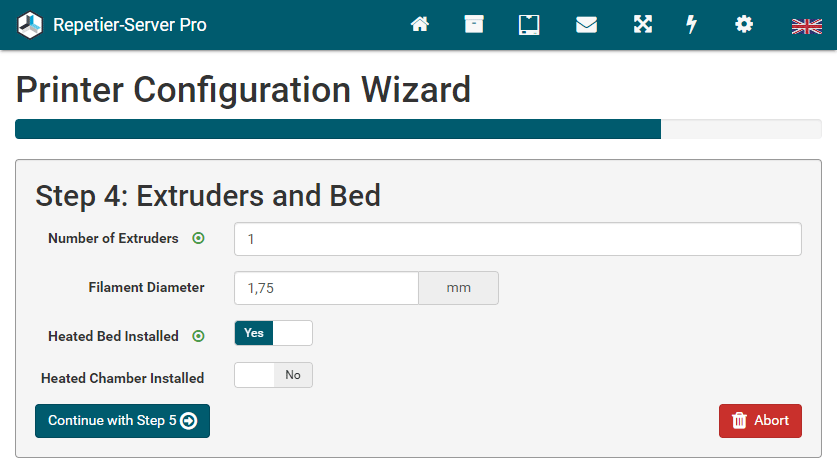
The normal rising/falling edge detection has a small amount of synchronisation built into the detection. by servicing the attached peripheral generating the interrupt).
REPETIER SERVER POWER SUPPLY SCRIPT SOFTWARE
Level interrupts maintain the interrupt status until the level has been cleared by system software (e.g. Several interrupt generation sources are configurable: InterruptsĮach GPIO pin, when configured as a general-purpose input, can be configured as an interrupt source to the ARM. The default pull states are also applied, which are detailed in the alternate function table in the ARM peripherals datasheet.
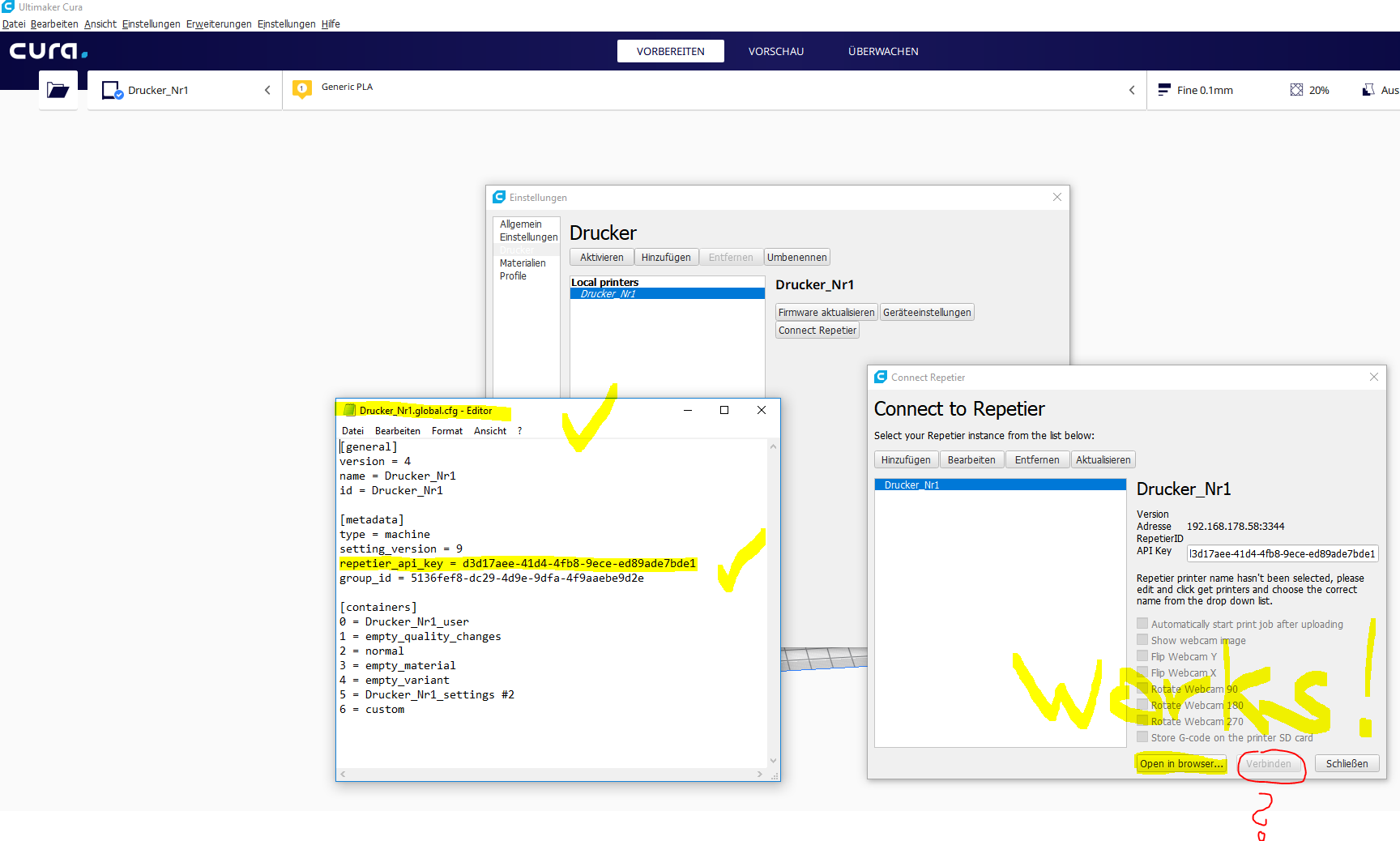
A selection of pins from Bank 0 is available on the P1 header on Raspberry Pi. Connection of a GPIO to a voltage higher than 3.3V will likely destroy the GPIO block within the SoC. On Raspberry Pi, all GPIO banks are supplied from 3.3V. Each of the three banks has its own VDD input pin. GPIO pins can be configured as either general-purpose input, general-purpose output, or as one of up to six special alternate settings, the functions of which are pin-dependent. When reading this page, reference should be made to the BCM2835 ARM peripherals data sheet, section 6. This page expands on the technical features of the GPIO pins available on BCM2835 in general. In addition to simple control, certain pins also perform certain functions such as communication via I2C, UART or SPI. GPIO pins - also called General Purpose Input Output - are the central interface between the Raspberry Pi to external devices and digital circuits. GPIO (General Purpose Input/Output) pins on the Raspberry Pi
